24
2022
-
08
Introduction of wear-resistant ceramic coating repair material
product name | Ceramic anti-corrosion and wear-resistant coating |
Model | LJ-TCNM117 |
Specification | A:10KG/barrel, B:10KG/barrel; A:B=2:1,30KG/set |
Production Date | See certificate in box |
Package | 30KG/set, 1set/carton |
Effect | Environmentally friendly wear-resistant lining material, non-flammable, safe to use, super wear-resistant, acid and alkali resistant, mainly used for pipeline lining anti-corrosion, absorption tower lining anti-corrosion, desulfurization tower wall anti-corrosion, spray layer beam anti-corrosion, ash powder , Pulverized coal pipeline anti-wear, etc. |
Ceramic particle ball repair process:
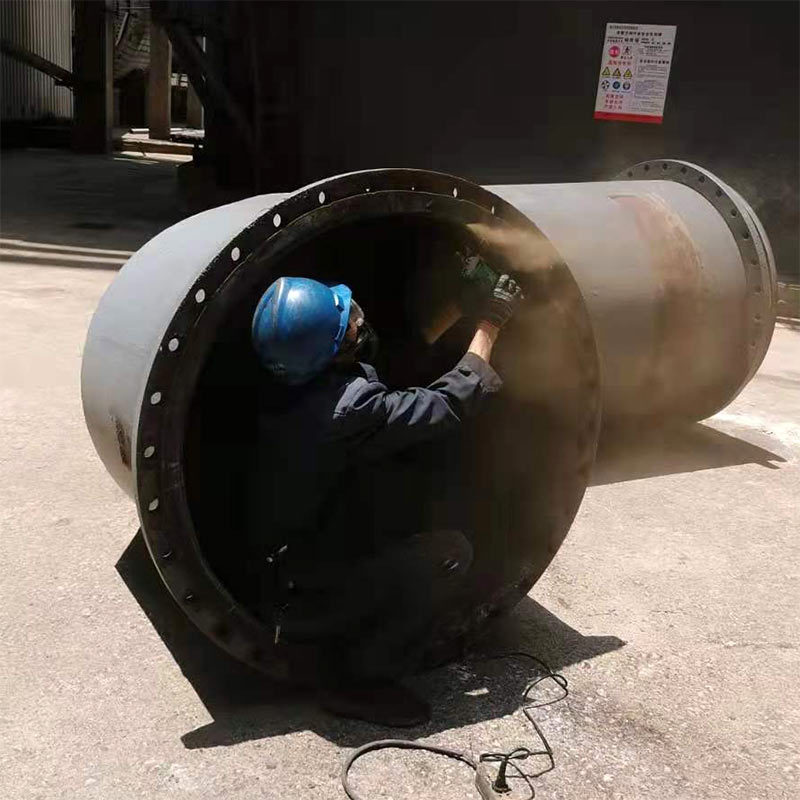
1. Surface treatment and roughening (remove dust, dirt, oil, grease and other attachments on the metal surface to reveal the metallic luster. If there is no sandblasting equipment, you can use the grinding method to roughen the surface to strengthen the repair material and metal adsorption capacity)

2. Mix components A and B evenly (the wear-resistant ceramic coating repair material is a two-component product, according to the weight ratio A:B=2:1; fully mix with a spatula, the mixing time is 3-5 minutes .At room temperature, the mixed material must be used up within 25 minutes, otherwise the material will become hard, which is not conducive to operation)
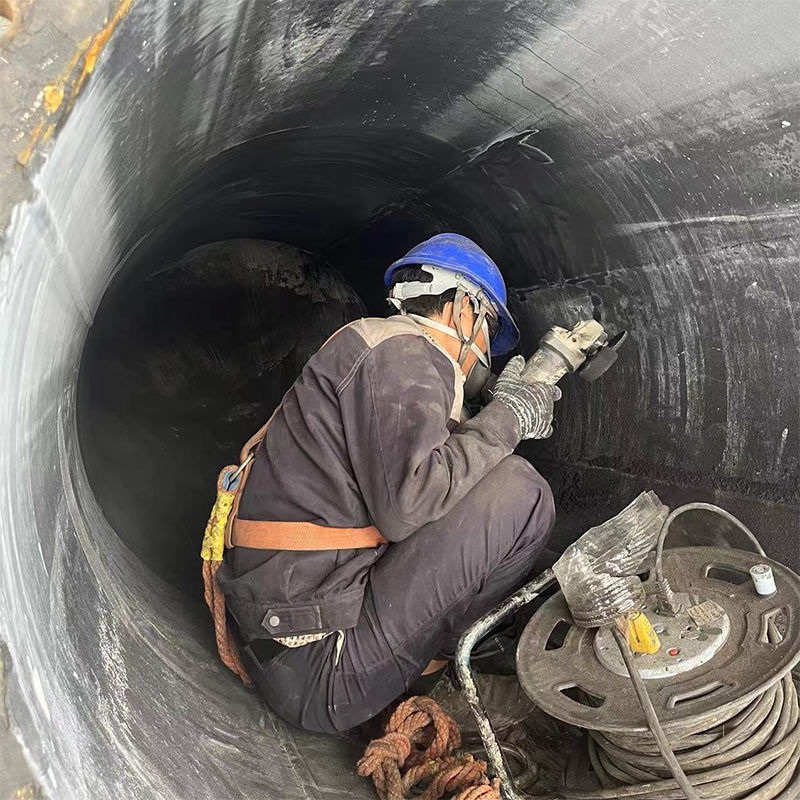
3. Coating construction (In order to facilitate smoothing the surface, use a hot tool spatula to scrape the mixed small particles of silicon carbide onto the surface to be repaired and protected. When semi-curing, pat the coating tightly and compact it, and iron it out. layer surface.)
Precautions:
1. The recommended construction temperature is 5-32°C, and the relative humidity is lower than 85%;
2. It is recommended that the thickness of the small particle silicon carbide wear-resistant coating be more than 2mm;
3. In winter, when the temperature is low, the curing time should be extended. If you need to speed up the curing, you can put the workpiece into the oven for 65 ℃ heating for 2 hours; Component A is heated or blown with hot air, softened and used, and does not respond to the properties of the material.)
4. For the repair of perforated or suspended parts, the mixed small particles of silicon carbide can be placed for 15 minutes. After the surface is initially solidified, the perforated or suspended parts can be filled, and the material will not sag and collapse.
Material quality requirements
Material physical properties:
Physical properties |
Anti-corrosion, wear-resistant |
Tensile strength Standard value≥25MPa |
82.13Mpa |
Flexural strength Standard value≥26MPa |
82.5Mpa |
Bond strength |
extremely strong |
Impact value Standard value≥0.41J/cm² |
0.9J/cm² |
Use temperature °C |
200℃ |
Barcol hardness Standard value≥40 |
90 |
Chemical properties |
Good acid and alkali resistance |
Repair case
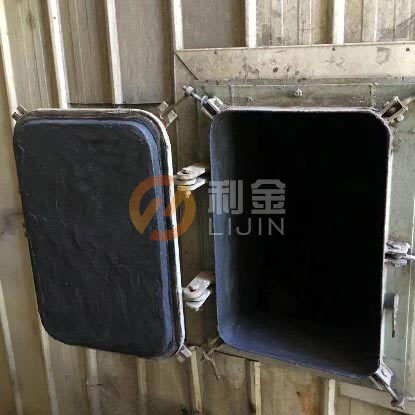
Absorption tower beam and flue repair
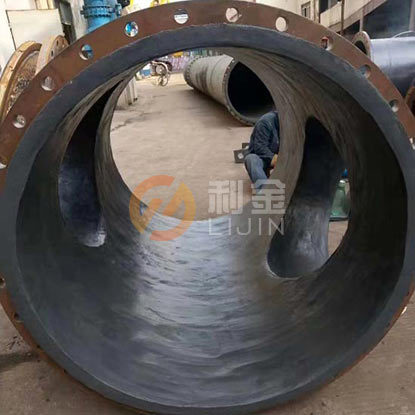
Four-way repair
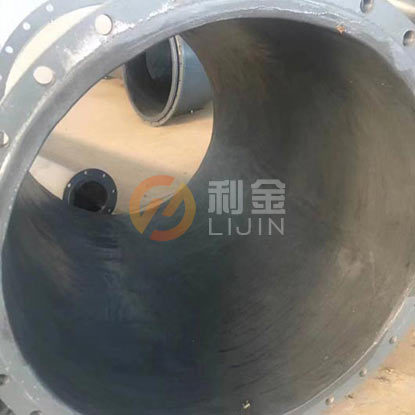
Straight pipe repair
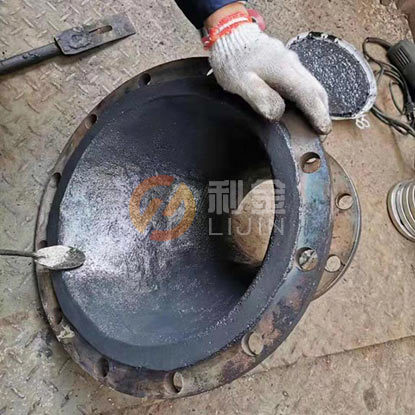
Head size repair
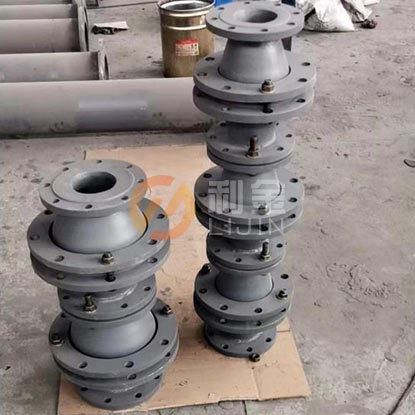
Head size repair
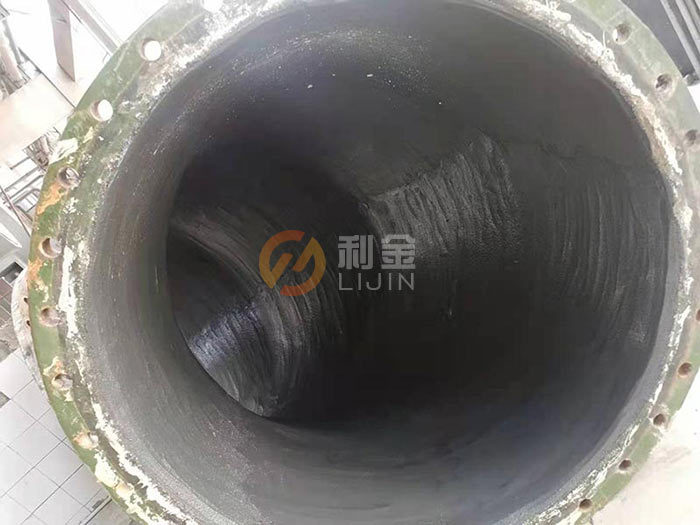
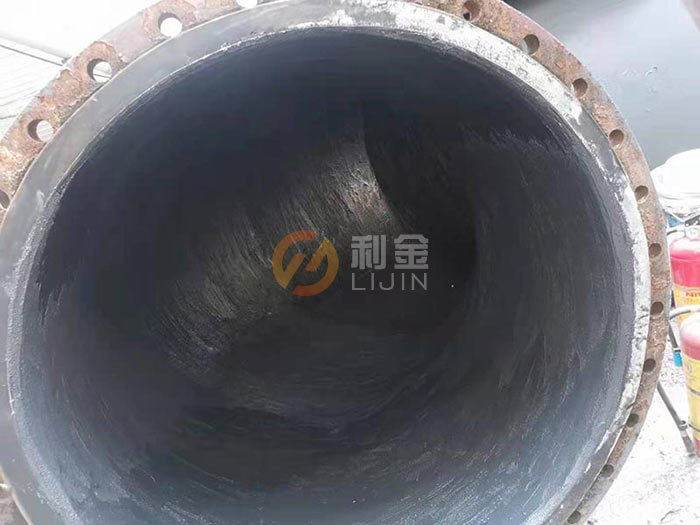
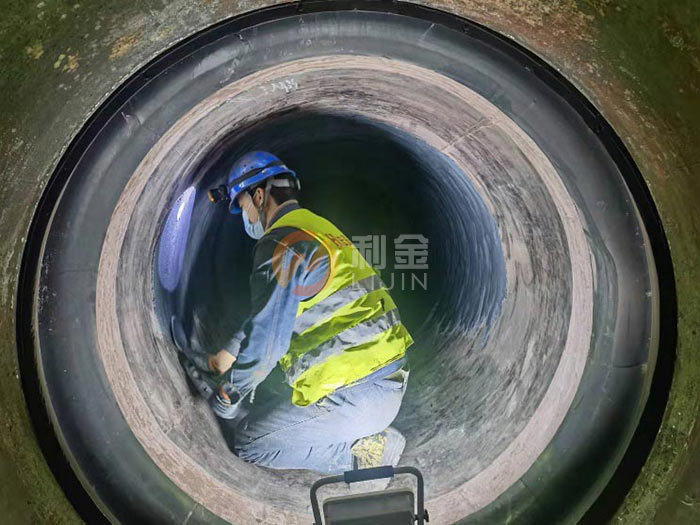
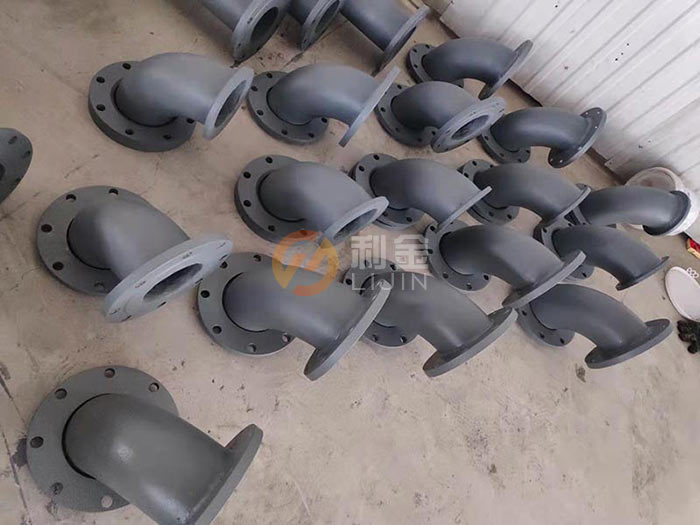
More industry applications
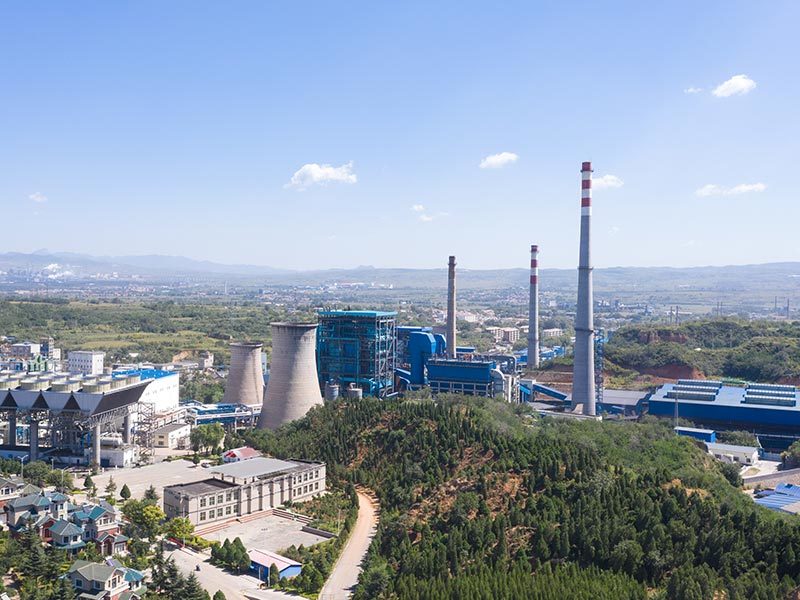
Power Industry
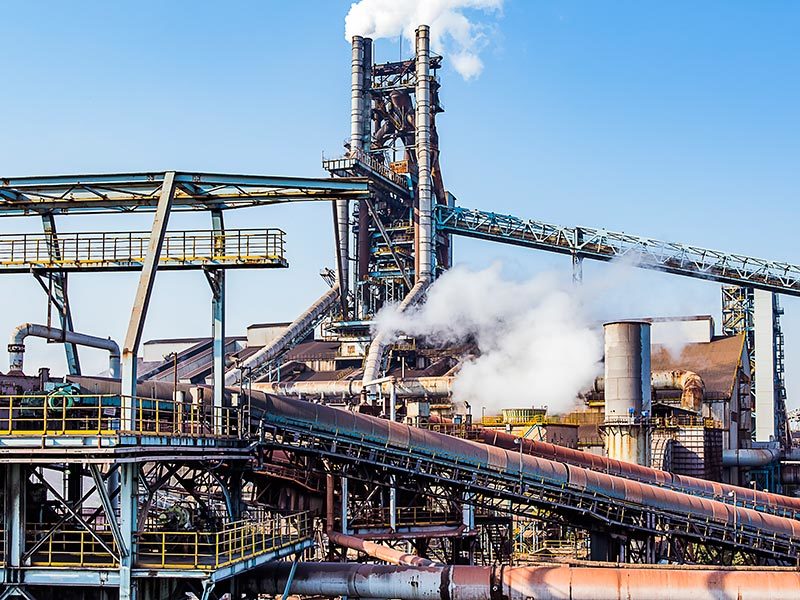
Chemical Industry
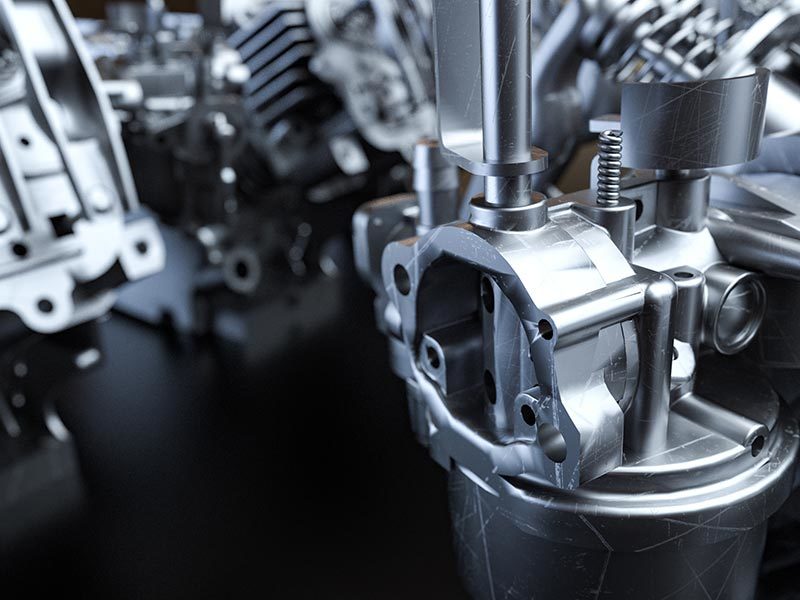
Machinery Industry
Product advantages
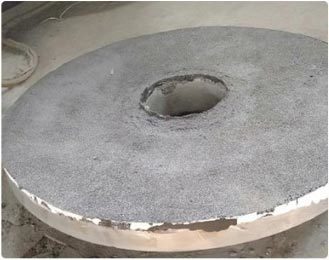
1. High overall strength
The main body is a composite material, and the wear resistance can reach 1-4 times that of medium carbon steel. The wear-resistant coating is firmly combined with the workpiece, and it is not easy to fall off and has excellent overall performance.
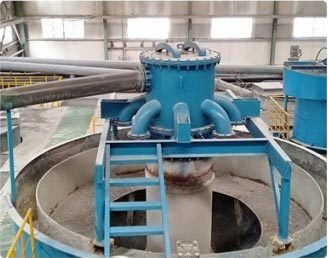
2. Strong applicability
Applicable to various acid and alkali conditions, as well as various high and low temperature conditions (~60°C-80°C)
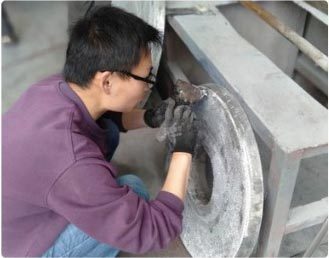
3. Fast repair speed
No need for technology and specific equipment to quickly repair all types of overcurrent erosion or corrosion equipment, reducing downtime.
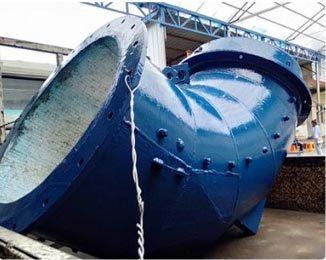
4. Low cost of repair
It can be repaired repeatedly, and the repair cost is only about 40% of the new part, and can save more time to improve production efficiency.
Related News
Email:sdlijin2022@163.com
Address:No. 5111, Kuiwen District, Weifang City, Shandong Province, China
Tel:+86-536-7242727
Phone:+86-188-6636-7765
Website:www.sdlijin.com
Copyright © 2022 Shandong Lijin New Material Technology Co., Ltd.